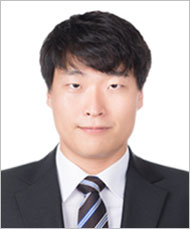
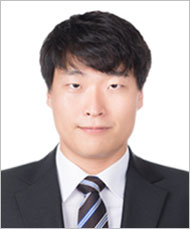
조구영
단국대학교
기계공학과
<표 3.1. 수소 생산기술의 분류>
<표 3.2. 수전해 수소의 분류>
• https://www.greenpeace.org/korea/update/17235/blog-ce-paris-climate-agreement-a-to-z/
• KISTEP 기술동향브리프 수소생산 김기봉, 김태경 한국과학기술기획평가원
• https://www.korea.kr/special/policyCurationView.do?newsId=148881562
• 국내IP 환경동향보고서 한국 재생에너지 동향과 대응정책, 환경부, 한국환경산업기술원
• 주요국의 수소경제 지원 정책과 시사점, 학국자원공학회지, 2020, vol.57, no.6, 통권 296호 pp. 629-639, 천강, 김진수
• Hydrogen Council, www.hydrogencouncil.com, 수소, 디지털과 만나다. 에너지 및 이동시스템의 새로운 기회 2018년 9월 수소 위원회 토론
• 수소 기술개발 로드맵
• 주요국 수소전략의 추진방향과 시사점, 2020년 8월 19일, vol. 20, No. 20, 안성배, 김종혁, 오태현, 이보람, 이현진, 대외경제정책연구원
• 에너지포커스 2019 겨울호, 16권 4호, 에너지경제연구원
• 고분자전해질 수전해 시스템 기술동향, 한상범, 공업화학 전망, 21권 3호, 2018
• 수소산업 수소경제의 새벽, 강동진, 박현욱, 장문수, 성정환, 현대차증권
• 고온수전해 수소 제조 연구 동향, 김선동, E2M, Vol. 31, No. 6, 2018
조구영
단국대학교
기계공학과
3장 수소생산
(1) 수소생산의 개요
1. 배경
2015년 파리기후변화협정(Paris Climate Argreement)는 지구온난화를 방지학 위하여 지구 평균 온도 상승을 2도 아래로 억제하고, 1.5도를 넘지 않도록 노력하는 것을 목표로 체결되었다.[1, 2] 195개의 협약가입국들은 온실가스 감축 목표를 제시해야 하며, 대한민국도 2030년까지 37% 감축을 목표로 제시하였고, 특히 2050년까지 탄소중립을 달성하겠다고 선언하였다. 스웨덴, 영국, 프랑스, 덴마크 뉴질랜드, 헝가리 6개 국가는 이미 탄소중립을 법제화하고 있으며, EU, 중국, 일본등도 2050년 탄소중립 목표를 선언하였다.[3] 따라서 전세계적으로 기존의 화석연료(석탄, 석유, 천연가스 등)를 사용한 전력생산을 대신하여 풍력, 태양광, 연료전지 등 다양한 재생에너지를 이용한 에너지(전력) 생산을 확대하기위해 노력하고 있다. 대한민국의 경우 신재생에너지 발전량은 꾸준하게 증가하였다.[4] 2004년 0.35TWh 에 불과하던 신재생에너지 발전량은 2019년 30.5TWh로 약 87배 증가하였다.[4] 세계적으로도 전세계 신재생에너지 발전량을 꾸준하게 증가하고 있으며, 대한민국을 포함한 중국, 일본, 독일 등이 재생에너지 발전량 비중 목표를 제시하였다.
대표적인 신재생에너지원인 태양광과 풍력은 친환경적이고 무한하다는 장점을 가지고 있으나, 날씨, 기후의 영향으로 설치 및 운영에 제약이 많기 때문에 불안정성을 내재하고 있다. 따라서, 날씨와 같은 외부의 영향을 받지않고 안정적으로 전력을 생산할 수 있는 연료전지와 수소가 주목을 받고 있으며 전세계적으로 많은 정책과 연구가 진행되고 있다. 미국은 에너지부(Department of Energy) 주관으로 수소경제로의 전환을 위한 ‘H2@Scale’ 프로젝트를 추진하고, 캘리포니아주에서만 2040년까지 수소차 100만대, 수소충전소 1,000개소 설치를 목표로 하고 있고, 중국은 2015년 ‘차이나 수소 이니셔티브’ 선언을 통해서 2030년까지 수소차 100만대, 수소충전소 1,000개르 목표로 설정했고, 일본도 ‘수소연료전지 전략로드맵’을 통해서 2030년까지 수소차 80만대, 수소버스 1,200대, 수소충전소 900개소, 가정용 연료전지 530만대, 수소 발전단가 17엔/kWh를 목표로 설정하였다.[5] 이에 따라 전세계적으로 수소 수요가 급증하고 있으며, 2050년 세계적인 수소 수요는 2020년의 10EJ 에서 78EJ로 증가할 것으로 예측되고 있다.[6]
특히 우리나라는 2019년 1월 세계 최고수준의 수소경제 선도국가로의 도약을 목표로 ‘수소경제 활성화 로드맵’을 시작으로 ‘수소경제 표전화 전략 로드맵 (2019년 4월), 수소 기술개발 로드맵 (2019년 10월), 수소 인프라 및 충전소 구축방안 (2019년 10월), 수소시범도시 추진전략 (2019년 10월)’ 등 후속조치가 발표되었다. 수소경제의 활성화 및 전환을 달성하기 위해서는 수소생산-저장-수송-활용 등을 모두 포함하는 수소경제 전주기 기술에 대한 연구개발이 필수적이며, 앞서 기술한 모든 상황들을 고려할 때 진정한 수소경제로 전환하기위한 가장 중요한 시작은 적절한 가격의 친환경 수소를 생산 및 공급하는 것이다.
2. 수소 생산기술의 분류
수소는 제약, 금속, 화학 및 전자산업 등 다양한 목적을 위해 이미 석유화학 등에서 여러 가지 방법을 통해서 생산되고 있었다. ‘수소 기술개발 로드맵’을 기준으로 수소 생산기술은 수소 생산을 위한 제조 원료와 제조 방법에 따라서 다음 <표. 3.1>과 같이 분류할 수 있다.[2, 7]
1. 배경
2015년 파리기후변화협정(Paris Climate Argreement)는 지구온난화를 방지학 위하여 지구 평균 온도 상승을 2도 아래로 억제하고, 1.5도를 넘지 않도록 노력하는 것을 목표로 체결되었다.[1, 2] 195개의 협약가입국들은 온실가스 감축 목표를 제시해야 하며, 대한민국도 2030년까지 37% 감축을 목표로 제시하였고, 특히 2050년까지 탄소중립을 달성하겠다고 선언하였다. 스웨덴, 영국, 프랑스, 덴마크 뉴질랜드, 헝가리 6개 국가는 이미 탄소중립을 법제화하고 있으며, EU, 중국, 일본등도 2050년 탄소중립 목표를 선언하였다.[3] 따라서 전세계적으로 기존의 화석연료(석탄, 석유, 천연가스 등)를 사용한 전력생산을 대신하여 풍력, 태양광, 연료전지 등 다양한 재생에너지를 이용한 에너지(전력) 생산을 확대하기위해 노력하고 있다. 대한민국의 경우 신재생에너지 발전량은 꾸준하게 증가하였다.[4] 2004년 0.35TWh 에 불과하던 신재생에너지 발전량은 2019년 30.5TWh로 약 87배 증가하였다.[4] 세계적으로도 전세계 신재생에너지 발전량을 꾸준하게 증가하고 있으며, 대한민국을 포함한 중국, 일본, 독일 등이 재생에너지 발전량 비중 목표를 제시하였다.
대표적인 신재생에너지원인 태양광과 풍력은 친환경적이고 무한하다는 장점을 가지고 있으나, 날씨, 기후의 영향으로 설치 및 운영에 제약이 많기 때문에 불안정성을 내재하고 있다. 따라서, 날씨와 같은 외부의 영향을 받지않고 안정적으로 전력을 생산할 수 있는 연료전지와 수소가 주목을 받고 있으며 전세계적으로 많은 정책과 연구가 진행되고 있다. 미국은 에너지부(Department of Energy) 주관으로 수소경제로의 전환을 위한 ‘H2@Scale’ 프로젝트를 추진하고, 캘리포니아주에서만 2040년까지 수소차 100만대, 수소충전소 1,000개소 설치를 목표로 하고 있고, 중국은 2015년 ‘차이나 수소 이니셔티브’ 선언을 통해서 2030년까지 수소차 100만대, 수소충전소 1,000개르 목표로 설정했고, 일본도 ‘수소연료전지 전략로드맵’을 통해서 2030년까지 수소차 80만대, 수소버스 1,200대, 수소충전소 900개소, 가정용 연료전지 530만대, 수소 발전단가 17엔/kWh를 목표로 설정하였다.[5] 이에 따라 전세계적으로 수소 수요가 급증하고 있으며, 2050년 세계적인 수소 수요는 2020년의 10EJ 에서 78EJ로 증가할 것으로 예측되고 있다.[6]
특히 우리나라는 2019년 1월 세계 최고수준의 수소경제 선도국가로의 도약을 목표로 ‘수소경제 활성화 로드맵’을 시작으로 ‘수소경제 표전화 전략 로드맵 (2019년 4월), 수소 기술개발 로드맵 (2019년 10월), 수소 인프라 및 충전소 구축방안 (2019년 10월), 수소시범도시 추진전략 (2019년 10월)’ 등 후속조치가 발표되었다. 수소경제의 활성화 및 전환을 달성하기 위해서는 수소생산-저장-수송-활용 등을 모두 포함하는 수소경제 전주기 기술에 대한 연구개발이 필수적이며, 앞서 기술한 모든 상황들을 고려할 때 진정한 수소경제로 전환하기위한 가장 중요한 시작은 적절한 가격의 친환경 수소를 생산 및 공급하는 것이다.
2. 수소 생산기술의 분류
수소는 제약, 금속, 화학 및 전자산업 등 다양한 목적을 위해 이미 석유화학 등에서 여러 가지 방법을 통해서 생산되고 있었다. ‘수소 기술개발 로드맵’을 기준으로 수소 생산기술은 수소 생산을 위한 제조 원료와 제조 방법에 따라서 다음 <표. 3.1>과 같이 분류할 수 있다.[2, 7]
분류 |
|||
수소 생산 | 연료이용 | 개질 반응 | 가스연료(LNG, LPG) 개질 |
부생가스 개질 | |||
합성연료(MeOH, DME) 개질 | |||
가스화 반응 | 석탄/펫코크 가스화 | ||
생물학적 전환 반응 | 생물학적 CO 전환 | ||
폐자원/바이오매스 이용 | 가연성 폐자원 가스화 | 가연성 폐자원 가스화 | |
생물학적 발효 | 생물학적 발효 | ||
바이오매스 가스화 | 바이오매스 가스화 | ||
물분해 | 전기 분해 (수전해) | 알칼리 수전해(AEC) | |
고분자전해질 수전해(PEMEC) | |||
고체산화물 수전해(SOEC) | |||
광 분해 | 광전기화학(PEC) | ||
광촉매 | |||
광생물학 | |||
열 분해 | 열화학사이클 | ||
레독스사이클 | |||
초고온가스로 | 초고온가스로 (원자력) |
○ 개질 반응을 이용한 수소 생산
개질 반응을 이용한 수소 생산은 천연가스, 석유, 석탄 등 탄화수소로 이루어진 화석연료를 제조원료로 개질 반응을 이용하여 수소를 생산한다. 수소 생산에 이용되는 개질 반응으로는 수증기 개질(Steam reforming), 부분 산화(Partial oxidation), 건식 개질(Dry reforming), 열분해(Thermal decomposition) 반응 등이 있으며, 수증기 개질이 가장 널리 이용된다.[2] 수증기 개질은 700도 ~ 900도의 온도에서 수증기와 메탄(CH4)를 반응시켜 수소를 생산하는 방식으로 다음과 같은 대표적인 화학반응식을 통해서 수소를 생산한다.


수증기 개질은 기술적 완성도가 높고 상대적으로 생산가격이 저렴하며 대량의 수소를 생산할 수 있다는 장점이 있지만, 화석연료를 사용하기 때문에 필연적으로 CO2 가 부산물로서 생산되며 화석연료의 수송과정까지 고려하면 더욱 많은 CO2가 발생한다는 단점이 존재한다. 개질 반응을 이용하여 생산한 수소는 수소 생산과정에서 온실가스가 함께 발생하기 때문에 회색수소/그레이수소(grey hydrogen)라고 부른다.
개질 반응을 이용한 수소 생산에 탄소 포집/활용 및 저장 공정(CCUS: Carbon Capture Utilization and Storage) 기술을 사용하여 천연가스 개질 혹은 부생수소 생산 시 발생하는 온실가스의 대기 유입을 방지할 수 있으며, 이러한 후처리 과정을 거쳐 생산한 수소를 청색수소/블루수소(blue hydrogen)이라고 부른다. [8]
○ 부생 수소
부생 수소는 나프타 분해 공정, 클로르-알칼리 공정, 탈수소 공정이나 제철 공정에서 화학반응 중에 부수적으로 생산되는 수소로서 우리나라 울산, 여수, 대산 등 석유화학단지에서 생산되며, 2016년 기준 171만톤의 수소가 생산되었다.[9] 부생수소는 타공정에서 발생하는 폐가스를 활용하므로 수소 생산을 위한 추가 투자가 발생하지 않아 경제성이 우수하다. 하지만, 수소 생산량에 있어 한계가 존재하며, 지역적으로 편중되어 있고, 공급변동성이 크며, 운송비용이 높고, 순도를 높이기 위한 추가적인 공정이 필요하다는 단점이 있다.
○ 수전해 수소
수전해 수소는 전기화학 반응을 이용하여 물을 전기분해하여 수소를 생산하는 기술로서, 대표적인 수전해 생산방식은 위 <표 3.1>에 나온것과 같이 알칼리 수전해(Alkaline Electrolysis Cell), 고분자전해질 수전해(Proton Exchange Membrane Electrolysis Cell), 고체산화물 수전해(Solid Oxide Electrolysis Cell)로 분류되며, 다음 <표 3.2>와 같이 비교가 가능하다.[2, 10]
개질 반응을 이용한 수소 생산은 천연가스, 석유, 석탄 등 탄화수소로 이루어진 화석연료를 제조원료로 개질 반응을 이용하여 수소를 생산한다. 수소 생산에 이용되는 개질 반응으로는 수증기 개질(Steam reforming), 부분 산화(Partial oxidation), 건식 개질(Dry reforming), 열분해(Thermal decomposition) 반응 등이 있으며, 수증기 개질이 가장 널리 이용된다.[2] 수증기 개질은 700도 ~ 900도의 온도에서 수증기와 메탄(CH4)를 반응시켜 수소를 생산하는 방식으로 다음과 같은 대표적인 화학반응식을 통해서 수소를 생산한다.
수증기 개질은 기술적 완성도가 높고 상대적으로 생산가격이 저렴하며 대량의 수소를 생산할 수 있다는 장점이 있지만, 화석연료를 사용하기 때문에 필연적으로 CO2 가 부산물로서 생산되며 화석연료의 수송과정까지 고려하면 더욱 많은 CO2가 발생한다는 단점이 존재한다. 개질 반응을 이용하여 생산한 수소는 수소 생산과정에서 온실가스가 함께 발생하기 때문에 회색수소/그레이수소(grey hydrogen)라고 부른다.
개질 반응을 이용한 수소 생산에 탄소 포집/활용 및 저장 공정(CCUS: Carbon Capture Utilization and Storage) 기술을 사용하여 천연가스 개질 혹은 부생수소 생산 시 발생하는 온실가스의 대기 유입을 방지할 수 있으며, 이러한 후처리 과정을 거쳐 생산한 수소를 청색수소/블루수소(blue hydrogen)이라고 부른다. [8]
○ 부생 수소
부생 수소는 나프타 분해 공정, 클로르-알칼리 공정, 탈수소 공정이나 제철 공정에서 화학반응 중에 부수적으로 생산되는 수소로서 우리나라 울산, 여수, 대산 등 석유화학단지에서 생산되며, 2016년 기준 171만톤의 수소가 생산되었다.[9] 부생수소는 타공정에서 발생하는 폐가스를 활용하므로 수소 생산을 위한 추가 투자가 발생하지 않아 경제성이 우수하다. 하지만, 수소 생산량에 있어 한계가 존재하며, 지역적으로 편중되어 있고, 공급변동성이 크며, 운송비용이 높고, 순도를 높이기 위한 추가적인 공정이 필요하다는 단점이 있다.
○ 수전해 수소
수전해 수소는 전기화학 반응을 이용하여 물을 전기분해하여 수소를 생산하는 기술로서, 대표적인 수전해 생산방식은 위 <표 3.1>에 나온것과 같이 알칼리 수전해(Alkaline Electrolysis Cell), 고분자전해질 수전해(Proton Exchange Membrane Electrolysis Cell), 고체산화물 수전해(Solid Oxide Electrolysis Cell)로 분류되며, 다음 <표 3.2>와 같이 비교가 가능하다.[2, 10]
구분 | 알칼라인 수전해 (AEC) |
고분자전해질 수전해 (PEMEC) |
고체산화물 수전해 (SOEC) |
반응식 | 2OH-→H2O+2e-+0.5O2 | 2H++2e-→H2 | H2O+2e-→H2+O2- |
2H2O+2e-→2OH-+H2 | H2O→0.5O2+2H++2e- | O2-→0.5O2+2e- | |
전해질 | 알칼리수용액 (격막+25~30% KOH등) |
고분자전해질막 양이온교환막(Nafion) |
이온전도성고체산화물 (YSZ 등) |
작동온도 | 60도~90도 | 20도~100도 | 700도~1,000도 |
촉매 | Ni/Fe 등 | Pt, Ir 등 | Ni, doped 세라믹 등 |
시동시간 | 1~5 min | <10 s | 15 min |
스택효율 (% LHV) |
63~71 | 60~68 | 100 |
시스템 효율 (% LHV) |
51~60 | 46~60 | 76~81 |
내구성 (1,000h) |
55~120 | 60~1,000 | 8~20 |
위 3가지 대표적인 수전해 반응중 알칼라인 수전해는 가장 먼저 상용화되었으며, 저가 소재를 사용하고, 대면적/대형화가 가능할 정도로 기술적 성숙도도 높다.[9] 고분자전해질 수전해 또한 대면적/대형화가 가능하지만, 귀금속 촉매를 사용해야하고, 아직 기술적 성숙도가 알칼리 수전해에 비해서 부족하다. 고체산화물 수전해는 수소 생산효율은 가장 높지만 현재 연구개발 단계에 머물러 있다.
수전해 반응을 이용한 수소 생산은 온실가스를 발생시키지 않고, 풍력/태양광/수력 등 재생에너지로 생산한 전기로 생산할 수 있기 때문에 녹색수소/그린수소(Green hydrogen) 또는 재생수소(Renewable hydrogen)라고 부르며 친환경적이지만, 높은 가격으로 인한 경제성 문제가 있다.
○ 원자력을 이용한 수소 생산
원자력을 이용한 수소 생산에서 가장 쉬운 방법은 원자력 발전소에서 나오는 전기를 이용하여 수전해를 통해서 수소를 대량으로 생산하는 것이다. 또한 원자력 발전소에서 나오는 고온의 열을 이용하면 고체산화물 수전해(SOEC)를 통해서 수소 생산 효율을 높일 수 있다.[9] 초고온 가스로에서 발생하는 고열을 직접 이용하여 열화학사이클 공정을 가동하면 가장 효율적인 수소 생산이 가능하다.[9] 미국, 일본, 유럽 등 주요 선진국에서는 연구가 지속적으로 진행되고 있으나 국내 연구는 미진하며, 기술 수준이 부족하다.[9]
○ 그 외 다양한 기술을 이용한 수소 생산
위에 <표 3.1.>에 나온 것처럼 이산화티타늄(TiO2)에 백금(Pt)를 코팅한 광촉매를 물에 분산시켜 태양광을 받아서 수소와 산소로 분해하는 광촉매 공정, 반도체물질을 광전극으로 활용하여 태양광으로 물을 수소와 산소로 분해하는 광전기화학소자를 이용하여 태양광으로부터 수소생산하는 기술이 있다. 또한 태양광을 이용하여 물로부터 수소를 생산하는 미생물을 활용하는 등 생물학적으로 수소를 생산하는 기술도 있다. 이러한 수소 생산방법등은 태양광과 물만 있으면 녹색수소 생산이 가능하다는 장점을 가지고 있지만, 아직 연구개발 초기 단계에 머물러 있어 대량양산에 있어서 한계를 가지고 있다. [9]
(2) 수소생산 관련 기술 및 산업 동향
앞에서 살펴본 것과 같이 수소 생산을 위한 다양한 방법이 있으나, 현재는 녹색수소(그린수소)를 생산하면서 대량양산이 가능한 수전해 기술이 각광받고 있는 분야이 다. 전세계 수전해 수소 시장은 2020년 84억 달러에서 2024년 176억 달러로 연평균 20.3% 고성장이 예상되며, 이에 따라서 신규 수전해 설비 설치 현황도 2018년 이전 연평균 10MW에서 2019년 25.4MW, 2023년 1,433MW로 급격한 성장이 예상되고 있다. 특히 이러한 수전해 설비는 알칼라인 수전해와 고분자전해질 수전해를 중심으로 수백 MW 급의 프로젝트로서 설치될 예정이다. [2] <표 3.2.>에 정리한 3가지 수전해 기술 중 알칼리 수전해 기술은 다공질 격막에 의해 산화전극과 환원전극이 분리되며, 25~30% 수산화나트륨이나, 수산화칼륨 수용액을 전해질(electrolyte)로 사용한다. 알칼리 수전해는 전해질의 높은 이온전도도때문에 전류밀도가 최대 0.45 A/cm2 정도로 낮고, 알칼리 전해질의 혼합 때문에 수소의 순도가 조금 낮다. (99.5~99.9%) 그러나 알칼리 전해질에는 저렴한 전이금속(니켈, 철 등)을 촉매로 사용할 수 있는 장점이 있어 다른 수전해 기술에 비해 초기비용이 저렴하다. 또한, 가장 성숙한 기술로서 MW급 수소발생장치에 적용되어 왔으며, 현재 다수의 업체에서 상용제품을 판매하고 있다. [10] 독일 Audi e-gas 플랜트에서 3개의 2MW(총 6MW)급 알칼라인 수전해 설비가 작동중에 있으며, 프랑스 McPhy는 20MW급 알칼라인 수전해 프로젝트를 진행중이고, Nouryon사, Gasunie사와 함께 네덜란드에도 수전해설비를 설치하였다. 노르웨이 NEL사는 미국에서 Southern California Gas사와 PtG 실증사업을 알칼라인 수전해설비(10Nm3/h)로 수행하였고, 노르웨이에서 150Nm3/h 설비를 설치하였다. 또한 EU는 2030년까지 수전해설비에 240억~420억 유로를 투자할 계획이다. 일본 Asahi-Kase사는 후쿠시마 수소에너지 연구단지(FH2R)를 통해 10MW급 알칼라인 수전해장치를 개발하였다. 우리나라에서는 수소에너젠이 400kW급 수전해 실증사업을 수행하고 2022년 1MW급 알칼라인 수전해 설비 실증 예정이다. 대표적인 기업으로는 유럽의 NEL Hydrogen, 일본의 Asahi Kasei, Hitachi Zosen이 있으며, 국내기업으로는 수소에너젠, EM 솔루션 등이 있으나 선진국 대비 핵심기술수준은 부족한 실정이다. [8, 10, 11]
고분자전해질 수전해 기술은 수소이온(양이온, Proton)을 전도할 수 있는 Nafion을 전해질로 이용하여 물을 전기분해하는 기술이다. 전해질로 사용하는 양이온교환막은 수소이온이 잘 분리될 수 있는 강한 산성의 얇은 막이다. 산성이기 때문에 고가의 촉매를 사용해야하며, 환원전극에는 carbon black과 Pt를 촉매로 사용하고 산화전극에는 IrOx 촉매를 사용한다. 고분자전해질 수전해는 고가의 귀금속 촉매 때문에 초기 시설비가 비싸지만, 다른 수전해 기술에 비해 전류밀도가 높아서 스택 및 시스템이 작고, 시동시간이 빠르며, 고순도 수소를 생산할 수 있다. 고분자전해질 수전해기술은 현재 상업화된 제품이 판매되고 있고 MW급 수전해 장치의 상업화도 진행되고 있다. 아직 상업화 초기단계에 있는 고분자전해질 수전해는 생산단가 감소, 안정성 증대 등을 통한 연구가 지속적으로 필요하다. [10] 고분자전해질 수전해의 상용화를 위한 연구로 높은 이온전도도를 가지면서도 내구성이 우수한 전해질(양이온교환막)에 관한 연구가 활발하게 진행되고 있다. 특히, 강화막을 적용하여 전해질의 두께를 감소시켜 전해질을 통한 이온전도 과정에서 발생하는 저항손실을 최소화하면서도 내구성을 향상시키는 연구가 진행되었다. [10] 또한, 촉매의 성능과 내구성을 향상시키기 위한 연구가 활발히 진행되고 있다. 촉매는 고분자전해질 수전해의 산화전극에서 발생하는 산소발생반응(Oxygen Evolution Reaction, OER)에서 주로 발생하며, OER 반응에서 활성화에너지를 감소시키기위한 물질/구조 촉매에 대한 연구가 진행고 있다. RuO2, IrO2, IrRuOx, RuOxNb1-xO2, 등 다양한 촉매에 관한 연구가 진행되고 있다. [10] 고분자전해질 수전해의 산성 특성과 산화전극의 높은 전위로 인해 안정적인 촉매담지체에 대한 연구가 수행되고 있다. 주로 티타늄 및 주석 계열의 전도성산화물 이용한 연구가 진행되었다. [10] 프랑스의 Air Liquide사는 캐나다의 20MW급 고분자전해질 수전해 설비를 도입하였고, 국내에서는 ㈜엘켐텍이 3,000cm2 대면적 고분자전해질 수전해 스택 상용화에 성공하였고, 다수의 실증연구에 참여하고 있으며, 2022년 1MW 고분자전해질 수전해 설비 실증에 참여할 예정이다. 대표적인 기업으로는 유럽의 Siemens, ITM Power, 미국의 Giner ELX, 캐나다의 Hydrogen, 일본의 Toshiba가 있으며, 국내회사로는 ㈜엘켐텍이 있다. [8, 10, 11]
고체산화물 수전해기술은 다른 수전해 기술과 달리 매우 높은 고온 (700도~1,000 도)에서 작동한다. 이는 산소이온(O2-) 전도성 세라믹(고체산화물)을 전해질로 사용하기 때문이다. 고체산화물 수전해 기술은 미국에서 연구가 시작되었고 수소 생산을 위한 수증기가 높은 작동온도 때문에 기체상태를 유지하기 때문에 상변화에 기인한 잠열 손실이 없어 매우 높은 에너지효율 (80% 이상)을 가지며, 높은 전류밀도 (1A/cm2)를 가진다. 그러나 작동온도가 높기 때문에 시동시간이 길고, 열응력 등으로 인한 문제가 있으며, 아직 연구초기 단계에 있다. 높은 에너지효율과 CO2+H2O의 동시 분해를 통한 합성가스 제조도 가능하기 때문에 지속적인 연구개발이 이루어 지고 있다. [10] 미국은 2005년부터 DOE Nuclear Hdyrogenn Initiative (NHI) 프로그램을 통해 4세대 고온원자로와 연계된 열화학적 방법 및 고온수전해 방법을 통한 수소제조 기술에 대한 타당성 검증을 실시해 왔다 [12]. 2009년 말에는 NHI 프로그램이 종료된 뒤 Next Generation Nuclear Plant 을 통해 고온수전해 수소 제조방식을 통해 대량 수소를 제조하는 연구가 계속 진행되어 왔다. Idaho National Lab.(INL) 및 Fuelcell Energy에서 중심으로 연구 개발을 추진중에 있으며, INL은 고온수전해 연구를 주도적으로 수행해 온 대표 연구기관으로 NREL, PNNL, SNL과 같은 National Lab과 파트너로서 연구를 추진하고 있다. Fuelcell Energy는 Versa Power Systems의 셀 소재/공정 기술과 NETL의 stack scale up, power system integration 기술을 기반으로 연구 개발을 추진 중이며 수소 제조 비용으로 $2/kg 이하로 제조하는 것을 목표로 하고 있다 [12]. 현재 달성한 연구의 수준은 5cm × 5cm × 0.03cm 단위셀(Ni-YSZ/YSZ/ LSCF)로 전류밀도 1.0 및 2.0 A/cm2 에서 각각 1.3 및 3.5%/1,000 h 의 열화율을 달성하였다. [12]
유럽은 2002년~2006년 European Hi2H2 컨소시엄에서 시작하여 프랑스 CEA, 덴마크 DTU-RISO, 덴마크 Topsoe, 네덜란드 ECN, 독일 EIFER, 독일 DLR, 프랑스 Helion, 영국 Imperial College, 스위스 EMPA 등이 참여한 Innovative Solid Oxide Electrolyser Stack for Efficient and Reliable Hydrogen Production (2007년~2013년)을 통해 추진되었다. 2008년부터 Fuel Cells and Hydrogen Joint Undsertaking을 통해 진행되는 통합 과학 기술연구 예산인 Framework Programme for Research (FP 6 and 7) 및 Horizon 2020 (2014년~2020년)을 기반으로 수행중이다 [12] 덴마크 기업인 Topsoe는 고체산화물연료전지 기술을 기반 전해질 및 전극 지지형 셀 개발을 추진해왔고, 금속지지형 셀 및 스택을 통해 작동온도를 낮춘 600도에서 구동되는 고온수전해 기술을 개발하고 있다. [12]. 최근 Technical University of Denmark 와 함께 CO2 또는 CO2+H2O 전해를 통해 99.995% 이상 고순도의 CO 기반 합성가스를 제조하는 전해 기술도 개발을 진행하고 있다. [12]
국내 연구는 2003년~2013년 수행된 21세기프론티어사업(고효율 수소에너지 제조·저장·이용 기술 개발사업)을 통해 본격적으로 시작되었다. 한국에너지기술연구원에서 평관형 고체산화물스택을 이용한 고온수전해 수소제조 기술을 확보하였다. [12]. 최근 2016년~2023년에 걸쳐 과기부·환경부·산업부가 공동으로 참여하여 신재생에너지 연계 고온·고압의 폐열을 활용하는 가역 연료전지-수전해 시스템 개발을 추진중이다. [12]
○ 원자력을 이용한 수소 생산
원자력을 이용한 수소 생산에서 가장 쉬운 방법은 원자력 발전소에서 나오는 전기를 이용하여 수전해를 통해서 수소를 대량으로 생산하는 것이다. 또한 원자력 발전소에서 나오는 고온의 열을 이용하면 고체산화물 수전해(SOEC)를 통해서 수소 생산 효율을 높일 수 있다.[9] 초고온 가스로에서 발생하는 고열을 직접 이용하여 열화학사이클 공정을 가동하면 가장 효율적인 수소 생산이 가능하다.[9] 미국, 일본, 유럽 등 주요 선진국에서는 연구가 지속적으로 진행되고 있으나 국내 연구는 미진하며, 기술 수준이 부족하다.[9]
○ 그 외 다양한 기술을 이용한 수소 생산
위에 <표 3.1.>에 나온 것처럼 이산화티타늄(TiO2)에 백금(Pt)를 코팅한 광촉매를 물에 분산시켜 태양광을 받아서 수소와 산소로 분해하는 광촉매 공정, 반도체물질을 광전극으로 활용하여 태양광으로 물을 수소와 산소로 분해하는 광전기화학소자를 이용하여 태양광으로부터 수소생산하는 기술이 있다. 또한 태양광을 이용하여 물로부터 수소를 생산하는 미생물을 활용하는 등 생물학적으로 수소를 생산하는 기술도 있다. 이러한 수소 생산방법등은 태양광과 물만 있으면 녹색수소 생산이 가능하다는 장점을 가지고 있지만, 아직 연구개발 초기 단계에 머물러 있어 대량양산에 있어서 한계를 가지고 있다. [9]
(2) 수소생산 관련 기술 및 산업 동향
앞에서 살펴본 것과 같이 수소 생산을 위한 다양한 방법이 있으나, 현재는 녹색수소(그린수소)를 생산하면서 대량양산이 가능한 수전해 기술이 각광받고 있는 분야이 다. 전세계 수전해 수소 시장은 2020년 84억 달러에서 2024년 176억 달러로 연평균 20.3% 고성장이 예상되며, 이에 따라서 신규 수전해 설비 설치 현황도 2018년 이전 연평균 10MW에서 2019년 25.4MW, 2023년 1,433MW로 급격한 성장이 예상되고 있다. 특히 이러한 수전해 설비는 알칼라인 수전해와 고분자전해질 수전해를 중심으로 수백 MW 급의 프로젝트로서 설치될 예정이다. [2] <표 3.2.>에 정리한 3가지 수전해 기술 중 알칼리 수전해 기술은 다공질 격막에 의해 산화전극과 환원전극이 분리되며, 25~30% 수산화나트륨이나, 수산화칼륨 수용액을 전해질(electrolyte)로 사용한다. 알칼리 수전해는 전해질의 높은 이온전도도때문에 전류밀도가 최대 0.45 A/cm2 정도로 낮고, 알칼리 전해질의 혼합 때문에 수소의 순도가 조금 낮다. (99.5~99.9%) 그러나 알칼리 전해질에는 저렴한 전이금속(니켈, 철 등)을 촉매로 사용할 수 있는 장점이 있어 다른 수전해 기술에 비해 초기비용이 저렴하다. 또한, 가장 성숙한 기술로서 MW급 수소발생장치에 적용되어 왔으며, 현재 다수의 업체에서 상용제품을 판매하고 있다. [10] 독일 Audi e-gas 플랜트에서 3개의 2MW(총 6MW)급 알칼라인 수전해 설비가 작동중에 있으며, 프랑스 McPhy는 20MW급 알칼라인 수전해 프로젝트를 진행중이고, Nouryon사, Gasunie사와 함께 네덜란드에도 수전해설비를 설치하였다. 노르웨이 NEL사는 미국에서 Southern California Gas사와 PtG 실증사업을 알칼라인 수전해설비(10Nm3/h)로 수행하였고, 노르웨이에서 150Nm3/h 설비를 설치하였다. 또한 EU는 2030년까지 수전해설비에 240억~420억 유로를 투자할 계획이다. 일본 Asahi-Kase사는 후쿠시마 수소에너지 연구단지(FH2R)를 통해 10MW급 알칼라인 수전해장치를 개발하였다. 우리나라에서는 수소에너젠이 400kW급 수전해 실증사업을 수행하고 2022년 1MW급 알칼라인 수전해 설비 실증 예정이다. 대표적인 기업으로는 유럽의 NEL Hydrogen, 일본의 Asahi Kasei, Hitachi Zosen이 있으며, 국내기업으로는 수소에너젠, EM 솔루션 등이 있으나 선진국 대비 핵심기술수준은 부족한 실정이다. [8, 10, 11]
고분자전해질 수전해 기술은 수소이온(양이온, Proton)을 전도할 수 있는 Nafion을 전해질로 이용하여 물을 전기분해하는 기술이다. 전해질로 사용하는 양이온교환막은 수소이온이 잘 분리될 수 있는 강한 산성의 얇은 막이다. 산성이기 때문에 고가의 촉매를 사용해야하며, 환원전극에는 carbon black과 Pt를 촉매로 사용하고 산화전극에는 IrOx 촉매를 사용한다. 고분자전해질 수전해는 고가의 귀금속 촉매 때문에 초기 시설비가 비싸지만, 다른 수전해 기술에 비해 전류밀도가 높아서 스택 및 시스템이 작고, 시동시간이 빠르며, 고순도 수소를 생산할 수 있다. 고분자전해질 수전해기술은 현재 상업화된 제품이 판매되고 있고 MW급 수전해 장치의 상업화도 진행되고 있다. 아직 상업화 초기단계에 있는 고분자전해질 수전해는 생산단가 감소, 안정성 증대 등을 통한 연구가 지속적으로 필요하다. [10] 고분자전해질 수전해의 상용화를 위한 연구로 높은 이온전도도를 가지면서도 내구성이 우수한 전해질(양이온교환막)에 관한 연구가 활발하게 진행되고 있다. 특히, 강화막을 적용하여 전해질의 두께를 감소시켜 전해질을 통한 이온전도 과정에서 발생하는 저항손실을 최소화하면서도 내구성을 향상시키는 연구가 진행되었다. [10] 또한, 촉매의 성능과 내구성을 향상시키기 위한 연구가 활발히 진행되고 있다. 촉매는 고분자전해질 수전해의 산화전극에서 발생하는 산소발생반응(Oxygen Evolution Reaction, OER)에서 주로 발생하며, OER 반응에서 활성화에너지를 감소시키기위한 물질/구조 촉매에 대한 연구가 진행고 있다. RuO2, IrO2, IrRuOx, RuOxNb1-xO2, 등 다양한 촉매에 관한 연구가 진행되고 있다. [10] 고분자전해질 수전해의 산성 특성과 산화전극의 높은 전위로 인해 안정적인 촉매담지체에 대한 연구가 수행되고 있다. 주로 티타늄 및 주석 계열의 전도성산화물 이용한 연구가 진행되었다. [10] 프랑스의 Air Liquide사는 캐나다의 20MW급 고분자전해질 수전해 설비를 도입하였고, 국내에서는 ㈜엘켐텍이 3,000cm2 대면적 고분자전해질 수전해 스택 상용화에 성공하였고, 다수의 실증연구에 참여하고 있으며, 2022년 1MW 고분자전해질 수전해 설비 실증에 참여할 예정이다. 대표적인 기업으로는 유럽의 Siemens, ITM Power, 미국의 Giner ELX, 캐나다의 Hydrogen, 일본의 Toshiba가 있으며, 국내회사로는 ㈜엘켐텍이 있다. [8, 10, 11]
고체산화물 수전해기술은 다른 수전해 기술과 달리 매우 높은 고온 (700도~1,000 도)에서 작동한다. 이는 산소이온(O2-) 전도성 세라믹(고체산화물)을 전해질로 사용하기 때문이다. 고체산화물 수전해 기술은 미국에서 연구가 시작되었고 수소 생산을 위한 수증기가 높은 작동온도 때문에 기체상태를 유지하기 때문에 상변화에 기인한 잠열 손실이 없어 매우 높은 에너지효율 (80% 이상)을 가지며, 높은 전류밀도 (1A/cm2)를 가진다. 그러나 작동온도가 높기 때문에 시동시간이 길고, 열응력 등으로 인한 문제가 있으며, 아직 연구초기 단계에 있다. 높은 에너지효율과 CO2+H2O의 동시 분해를 통한 합성가스 제조도 가능하기 때문에 지속적인 연구개발이 이루어 지고 있다. [10] 미국은 2005년부터 DOE Nuclear Hdyrogenn Initiative (NHI) 프로그램을 통해 4세대 고온원자로와 연계된 열화학적 방법 및 고온수전해 방법을 통한 수소제조 기술에 대한 타당성 검증을 실시해 왔다 [12]. 2009년 말에는 NHI 프로그램이 종료된 뒤 Next Generation Nuclear Plant 을 통해 고온수전해 수소 제조방식을 통해 대량 수소를 제조하는 연구가 계속 진행되어 왔다. Idaho National Lab.(INL) 및 Fuelcell Energy에서 중심으로 연구 개발을 추진중에 있으며, INL은 고온수전해 연구를 주도적으로 수행해 온 대표 연구기관으로 NREL, PNNL, SNL과 같은 National Lab과 파트너로서 연구를 추진하고 있다. Fuelcell Energy는 Versa Power Systems의 셀 소재/공정 기술과 NETL의 stack scale up, power system integration 기술을 기반으로 연구 개발을 추진 중이며 수소 제조 비용으로 $2/kg 이하로 제조하는 것을 목표로 하고 있다 [12]. 현재 달성한 연구의 수준은 5cm × 5cm × 0.03cm 단위셀(Ni-YSZ/YSZ/ LSCF)로 전류밀도 1.0 및 2.0 A/cm2 에서 각각 1.3 및 3.5%/1,000 h 의 열화율을 달성하였다. [12]
유럽은 2002년~2006년 European Hi2H2 컨소시엄에서 시작하여 프랑스 CEA, 덴마크 DTU-RISO, 덴마크 Topsoe, 네덜란드 ECN, 독일 EIFER, 독일 DLR, 프랑스 Helion, 영국 Imperial College, 스위스 EMPA 등이 참여한 Innovative Solid Oxide Electrolyser Stack for Efficient and Reliable Hydrogen Production (2007년~2013년)을 통해 추진되었다. 2008년부터 Fuel Cells and Hydrogen Joint Undsertaking을 통해 진행되는 통합 과학 기술연구 예산인 Framework Programme for Research (FP 6 and 7) 및 Horizon 2020 (2014년~2020년)을 기반으로 수행중이다 [12] 덴마크 기업인 Topsoe는 고체산화물연료전지 기술을 기반 전해질 및 전극 지지형 셀 개발을 추진해왔고, 금속지지형 셀 및 스택을 통해 작동온도를 낮춘 600도에서 구동되는 고온수전해 기술을 개발하고 있다. [12]. 최근 Technical University of Denmark 와 함께 CO2 또는 CO2+H2O 전해를 통해 99.995% 이상 고순도의 CO 기반 합성가스를 제조하는 전해 기술도 개발을 진행하고 있다. [12]
국내 연구는 2003년~2013년 수행된 21세기프론티어사업(고효율 수소에너지 제조·저장·이용 기술 개발사업)을 통해 본격적으로 시작되었다. 한국에너지기술연구원에서 평관형 고체산화물스택을 이용한 고온수전해 수소제조 기술을 확보하였다. [12]. 최근 2016년~2023년에 걸쳐 과기부·환경부·산업부가 공동으로 참여하여 신재생에너지 연계 고온·고압의 폐열을 활용하는 가역 연료전지-수전해 시스템 개발을 추진중이다. [12]
[Reference]
• https://www.greenpeace.org/korea/update/17235/blog-ce-paris-climate-agreement-a-to-z/
• KISTEP 기술동향브리프 수소생산 김기봉, 김태경 한국과학기술기획평가원
• https://www.korea.kr/special/policyCurationView.do?newsId=148881562
• 국내IP 환경동향보고서 한국 재생에너지 동향과 대응정책, 환경부, 한국환경산업기술원
• 주요국의 수소경제 지원 정책과 시사점, 학국자원공학회지, 2020, vol.57, no.6, 통권 296호 pp. 629-639, 천강, 김진수
• Hydrogen Council, www.hydrogencouncil.com, 수소, 디지털과 만나다. 에너지 및 이동시스템의 새로운 기회 2018년 9월 수소 위원회 토론
• 수소 기술개발 로드맵
• 주요국 수소전략의 추진방향과 시사점, 2020년 8월 19일, vol. 20, No. 20, 안성배, 김종혁, 오태현, 이보람, 이현진, 대외경제정책연구원
• 에너지포커스 2019 겨울호, 16권 4호, 에너지경제연구원
• 고분자전해질 수전해 시스템 기술동향, 한상범, 공업화학 전망, 21권 3호, 2018
• 수소산업 수소경제의 새벽, 강동진, 박현욱, 장문수, 성정환, 현대차증권
• 고온수전해 수소 제조 연구 동향, 김선동, E2M, Vol. 31, No. 6, 2018
![]() |