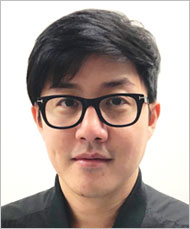
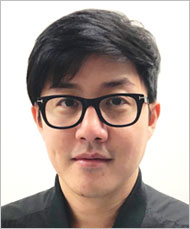
이윤호
울산대학교 기계공학부 교수
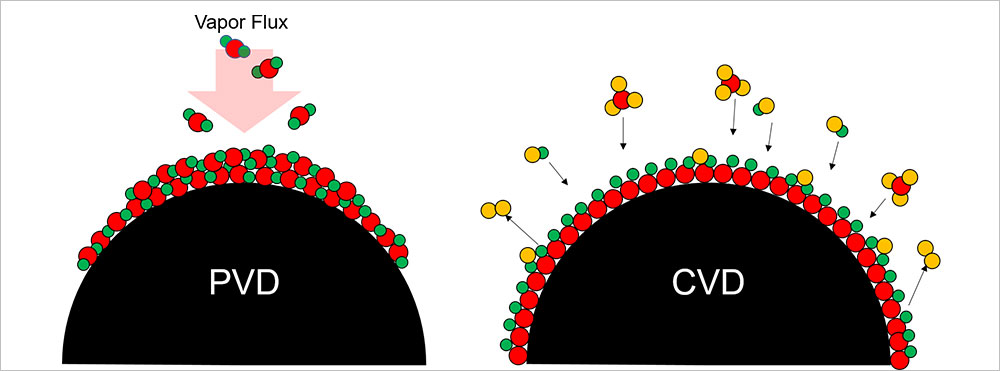
그림 1. PVD와 CVD의 원리 및 형성된 박막의 구조 차이
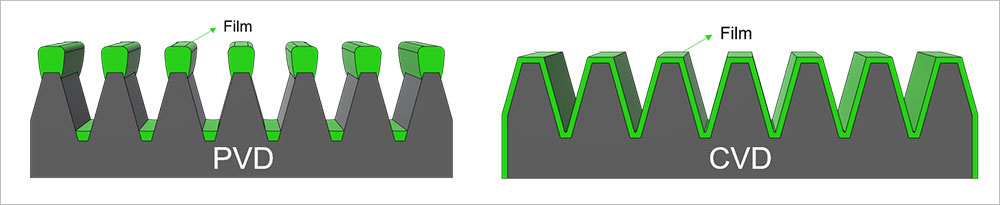
그림 2. PVD와 CVD의 원리 및 형성된 박막의 구조 차이 [1]
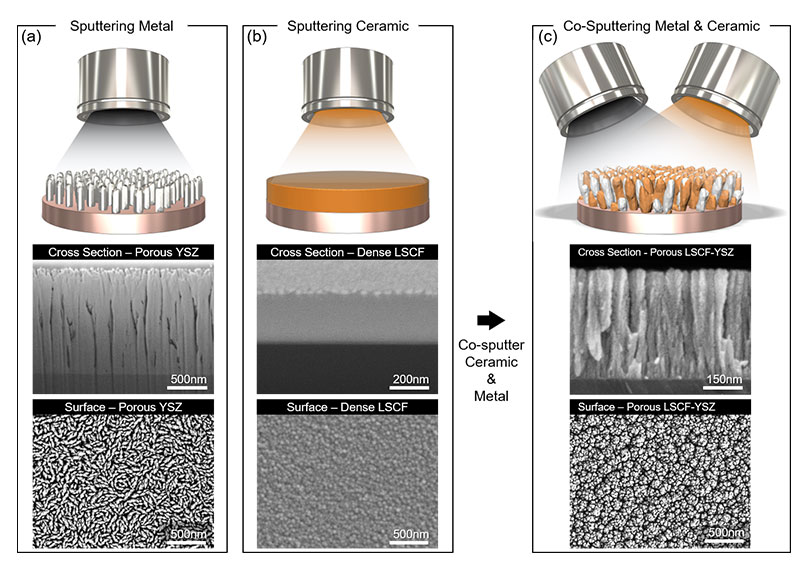
그림 3. 저진공 환경에서 스퍼터링한 (a)금속재료 박막 형상 (b)세라믹재료 박막 형상, (c)금속재료&세라믹재료 박막형상 [2]
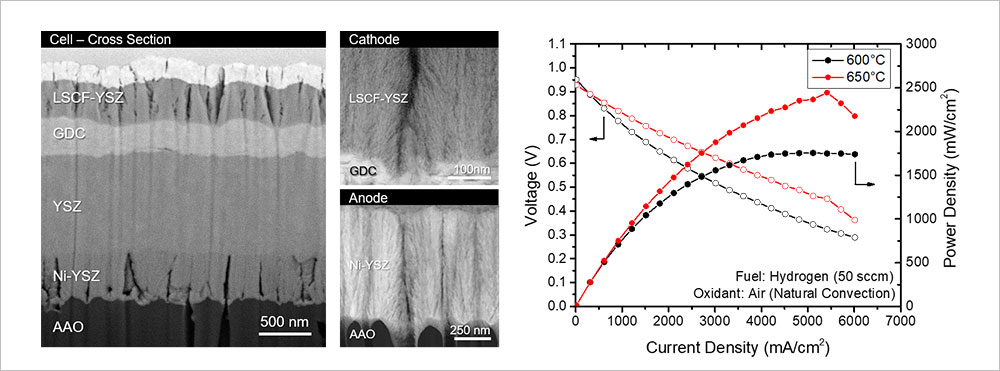
그림 4. 반도체 공정(스퍼터링)으로 제작된 셀의 전자현미경 단면 이미지(좌측), 전극 이미지 (중간), 성능 곡선 (우측) [2]
• Lee, Y. H.; Chang, I.; Cho, G. Y.; Park, J.; Yu, W.; Tanveer, W. H.; & Cha, S. W. Thin film solid oxide fuel cells operating below 600 C: a review. International Journal of Precision Engineering and Manufacturing-Green Technology 2018, 5, 441-453.
• Lee, Y. H.; Ren, H.; Wu, E. A.; Fullerton, E. E.; Meng, Y. S.; Minh, N. Q. All-Sputtered, Superior Power Density Thin-Film Solid Oxide Fuel Cells with a Novel Nanofibrous Ceramic Cathode. Nano Lett. 2020, 20, 2943−2949
• Lee, Y.-H.; Cho, G.-Y.; Chang, I.; Ji, S.; Kim, Y.-B.; Cha, S.-W. Platinum-Based Nanocomposite Electrodes for Low-Temperature Solid Oxide Fuel Cells with Extended Lifetime. J. Power Sources 2016, 307, 289−296.
이윤호
울산대학교 기계공학부 교수
반도체 기술과 고체산화물 연료전지
200년 가까이 되는 연료전지 역사상 지금처럼 많은 주목을 받아본 적은 아마도 없을 것이다. 그렇다면 과연 연료전지에는 어떠한 특징이 있기에 기술 변화의 변곡점에 서있는 2020년대 사회가 200년 전에 탄생한 기술에 이토록 주목하는 것일까? 그것을 파악하기 위해서는 우선 연료전지의 기본인 반응식을 알아볼 필요가 있다.
2H2 + O2 → 2H2O
(1) 즉 연료전지는 수소와 산소가 만나서 전기를 생산하고 물이 되는 간단한 반응이다. 물론 이러한 반응 사이에는 수소와 산소가 이온화되는 여러 단계의 과정이 존재하고 이 과정에서 생성된 이온과 전자가 각각 전해질과 전선을 통해 이동되는 복잡한 물질전달 메커니즘이 포함되어 있다. 하지만 반응식에서 주목할 점은 생성물에 탄소 산화물이 존재하지 않는다는 것이다. 우리에게 친숙한 대부분의 연료의 연소반응에는 항상 일산화, 이산화탄소가 생성물로 존재했던 것과는 매우 대조적이다. 또 한 가지 큰 특징은 연료전지를 통해 저 반응식이 역으로도 수행 될 수 있다는 점이다. 즉 연료전지는 수소와 산소가 만나 전기를 발생시킬 수도 있지만 물에 전기를 가하게 되면 수소와 산소로 분리되는 수전해도 가능하다. 이러한 두 가지 특징은 연료전지로 하여금 신재생에너지 발전의 코어 역할을 수행하게 한다.
우리는 이미 열역학 2법칙을 통해 식(1)의 정반응, 역반응 효율이 100%를 도달하지 못한다는 것을 잘 알고 있다. 즉 전기분해를 통해 생성된 수소와 산소를 다시 전기로 만드는 행위 자체는 열역학적으로 넌센스에 가깝다. 하지만 만약 이 행위가 풍력, 태양광, 수력 등의 신재생 에너지와 결합된다면 어떻게 될까? 신재생 에너지의 가장 큰 단점은 전기 발전에 있어 시공간의 제약이 있다는 점이다. 태양광을 예로 들면 일조량이 없는 저녁에는 발전량이 평균을 밑돌며 일조량이 강한 낮에는 초과 발전으로 인한 잉여 전력이 발생한다. 즉 대부분의 신재생 에너지는 수요에 의한 탄력적 발전이 아닌 환경에 의해 발전량이 강제되는 에너지 변환 시스템이다. 하지만 신재생 에너지를 연료전지와 결합하면 잉여 전력이 발생하는 낮에는 물을 전기분해하여 수소를 저장하고 저녁에는 생성된 수소로 부족한 전력 발전량을 보조할 수 있다. 즉 연료전지가 역으로도 동작한다는 것은 신재생 에너지의 시간, 날씨에 따라 불규칙적으로 변동하는 발전량을 전력 수요에 맞게 능동적으로 조절할 수 있다는 것을 시사한다. 따라서 연료전지 정반응(전력생산)과 역반응(수전해)의 효율은 신재생 에너지의 탄력적인 운용에 핵심이 될 수밖에 없다.
이러한 효율 극대화 측면에서 등장한 것이 고체산화물 연료전지이다. 고체산화물 연료전지는 모든 전극과 전해질이 고체산화물 연료전지로 이루어져 있으며 수소 이온이 고분자 전해질을 통해 전달되는 고분자막 연료전지와는 달리 산소 이온이 고체산화물 전해질을 통과한다. 고체산화물 전해질 내 산소 이온의 전달은 필연적으로 600~700oC 이상의 높은 온도를 요구하며 이러한 고온에서는 연료전지의 전극 촉매 반응이 활발해 지므로 고가의 귀금속 촉매가 요구되지 않는다. 또한 연료전지의 비가역성으로 인한 폐열의 온도가 상대적으로 높기 때문에 열병합 발전으로 인한 효율 향상을 기대할 수 있다. 다만 이러한 효율 및 재료에 대한 장점에도 불구하고 고분자막 연료전지와 비교하여 상대적 전력밀도가 낮기 때문에 단위 면적당 성능 향상을 목표로 꾸준한 연구가 진행되고 있다.
고체산화물 연료전지의 여러 성능 파라미터 중 가장 큰 영향을 미치는 것은 전극의 촉매성능과 전해질의 이온전달능력일 것이다. 따라서 고체산화물 개발에는 촉매의 교환전류밀도 및 전해질의 이온전도도를 향상시키기 위한 재료적 접근이 다수 이루어졌으며 우수한 전극 전해질 재료들이 등장하였다. 하지만 연료전지 성능을 결정짓는 지배방정식에는 전극과 전해질의 형상에 따른 파라미터들이 내재되어 있기 때문에 형상 제어를 통해서도 성능 및 효율 향상을 이끌어 낼 수 있다. 특히 전해질의 두께와 전극의 입자크기는 성능에 가장 큰 영향을 나타내는 형상 파라미터이므로 이 둘의 영향을 극대화 시키는 방향으로 고체산화물 연료전지 셀 구조를 설계 및 제작하면 동일한 재료 하에서도 성능 및 효율개선을 기대할 수 있다.
통상적으로 고체산화물 연료전지를 제작하는 공정은 도자기를 제작하는 방식과 유사하다. 고체산화물의 영어식 표현인 세라믹의 어원이 그리스어로 κεραμικός(keramikos) 즉 도자기임을 상기하자. 도자기를 가마에서 굽는 것과 마찬가지로 고체산화물 연료전지 역시 제작에 있어 1000oC 이상의 고온 열처리를 요구한다. 이 때문에 전극의 입자크기 및 전해질의 두께를 줄이는데 있어 명확한 한계가 존재한다. 반도체 공정은 반면에 전기소자의 고집적화를 가능케 한 일등공신으로 Å ~ nm 단위의 박막 및 입자 제작이 가능하다. 즉 반도체 공정을 통해 기존의 세라믹 공정 대비 더 얇은 전해질막, 더 작은 입자의 전극을 제작할 수 있으므로 고체산화물 연료전지의 구조를 혁신적으로 개선하여 효율 및 성능을 극대화 할 수 있다. 하지만 반도체 공정장비 마다 장단점이 다르고 초기에 높은 시설 투자비용 등이 발생하므로 신중한 공정장비 선택이 이루어져야 한다.
(1) 즉 연료전지는 수소와 산소가 만나서 전기를 생산하고 물이 되는 간단한 반응이다. 물론 이러한 반응 사이에는 수소와 산소가 이온화되는 여러 단계의 과정이 존재하고 이 과정에서 생성된 이온과 전자가 각각 전해질과 전선을 통해 이동되는 복잡한 물질전달 메커니즘이 포함되어 있다. 하지만 반응식에서 주목할 점은 생성물에 탄소 산화물이 존재하지 않는다는 것이다. 우리에게 친숙한 대부분의 연료의 연소반응에는 항상 일산화, 이산화탄소가 생성물로 존재했던 것과는 매우 대조적이다. 또 한 가지 큰 특징은 연료전지를 통해 저 반응식이 역으로도 수행 될 수 있다는 점이다. 즉 연료전지는 수소와 산소가 만나 전기를 발생시킬 수도 있지만 물에 전기를 가하게 되면 수소와 산소로 분리되는 수전해도 가능하다. 이러한 두 가지 특징은 연료전지로 하여금 신재생에너지 발전의 코어 역할을 수행하게 한다.
우리는 이미 열역학 2법칙을 통해 식(1)의 정반응, 역반응 효율이 100%를 도달하지 못한다는 것을 잘 알고 있다. 즉 전기분해를 통해 생성된 수소와 산소를 다시 전기로 만드는 행위 자체는 열역학적으로 넌센스에 가깝다. 하지만 만약 이 행위가 풍력, 태양광, 수력 등의 신재생 에너지와 결합된다면 어떻게 될까? 신재생 에너지의 가장 큰 단점은 전기 발전에 있어 시공간의 제약이 있다는 점이다. 태양광을 예로 들면 일조량이 없는 저녁에는 발전량이 평균을 밑돌며 일조량이 강한 낮에는 초과 발전으로 인한 잉여 전력이 발생한다. 즉 대부분의 신재생 에너지는 수요에 의한 탄력적 발전이 아닌 환경에 의해 발전량이 강제되는 에너지 변환 시스템이다. 하지만 신재생 에너지를 연료전지와 결합하면 잉여 전력이 발생하는 낮에는 물을 전기분해하여 수소를 저장하고 저녁에는 생성된 수소로 부족한 전력 발전량을 보조할 수 있다. 즉 연료전지가 역으로도 동작한다는 것은 신재생 에너지의 시간, 날씨에 따라 불규칙적으로 변동하는 발전량을 전력 수요에 맞게 능동적으로 조절할 수 있다는 것을 시사한다. 따라서 연료전지 정반응(전력생산)과 역반응(수전해)의 효율은 신재생 에너지의 탄력적인 운용에 핵심이 될 수밖에 없다.
이러한 효율 극대화 측면에서 등장한 것이 고체산화물 연료전지이다. 고체산화물 연료전지는 모든 전극과 전해질이 고체산화물 연료전지로 이루어져 있으며 수소 이온이 고분자 전해질을 통해 전달되는 고분자막 연료전지와는 달리 산소 이온이 고체산화물 전해질을 통과한다. 고체산화물 전해질 내 산소 이온의 전달은 필연적으로 600~700oC 이상의 높은 온도를 요구하며 이러한 고온에서는 연료전지의 전극 촉매 반응이 활발해 지므로 고가의 귀금속 촉매가 요구되지 않는다. 또한 연료전지의 비가역성으로 인한 폐열의 온도가 상대적으로 높기 때문에 열병합 발전으로 인한 효율 향상을 기대할 수 있다. 다만 이러한 효율 및 재료에 대한 장점에도 불구하고 고분자막 연료전지와 비교하여 상대적 전력밀도가 낮기 때문에 단위 면적당 성능 향상을 목표로 꾸준한 연구가 진행되고 있다.
고체산화물 연료전지의 여러 성능 파라미터 중 가장 큰 영향을 미치는 것은 전극의 촉매성능과 전해질의 이온전달능력일 것이다. 따라서 고체산화물 개발에는 촉매의 교환전류밀도 및 전해질의 이온전도도를 향상시키기 위한 재료적 접근이 다수 이루어졌으며 우수한 전극 전해질 재료들이 등장하였다. 하지만 연료전지 성능을 결정짓는 지배방정식에는 전극과 전해질의 형상에 따른 파라미터들이 내재되어 있기 때문에 형상 제어를 통해서도 성능 및 효율 향상을 이끌어 낼 수 있다. 특히 전해질의 두께와 전극의 입자크기는 성능에 가장 큰 영향을 나타내는 형상 파라미터이므로 이 둘의 영향을 극대화 시키는 방향으로 고체산화물 연료전지 셀 구조를 설계 및 제작하면 동일한 재료 하에서도 성능 및 효율개선을 기대할 수 있다.
통상적으로 고체산화물 연료전지를 제작하는 공정은 도자기를 제작하는 방식과 유사하다. 고체산화물의 영어식 표현인 세라믹의 어원이 그리스어로 κεραμικός(keramikos) 즉 도자기임을 상기하자. 도자기를 가마에서 굽는 것과 마찬가지로 고체산화물 연료전지 역시 제작에 있어 1000oC 이상의 고온 열처리를 요구한다. 이 때문에 전극의 입자크기 및 전해질의 두께를 줄이는데 있어 명확한 한계가 존재한다. 반도체 공정은 반면에 전기소자의 고집적화를 가능케 한 일등공신으로 Å ~ nm 단위의 박막 및 입자 제작이 가능하다. 즉 반도체 공정을 통해 기존의 세라믹 공정 대비 더 얇은 전해질막, 더 작은 입자의 전극을 제작할 수 있으므로 고체산화물 연료전지의 구조를 혁신적으로 개선하여 효율 및 성능을 극대화 할 수 있다. 하지만 반도체 공정장비 마다 장단점이 다르고 초기에 높은 시설 투자비용 등이 발생하므로 신중한 공정장비 선택이 이루어져야 한다.
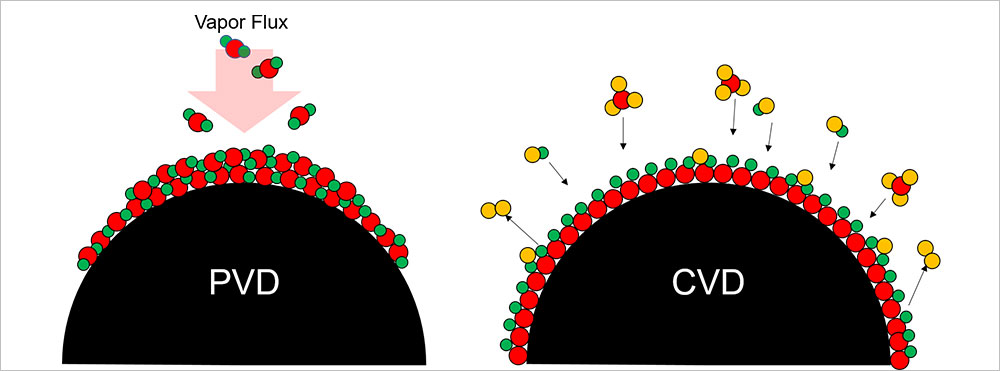
반도체 공정장비는 크게 물리기상증착법인 PVD, 화학기상증착법인 CVD로 나눌 수 있다. PVD는 진공상태에서 원하는 재료를 물리적인 힘 혹은 열에너지로 증발시켜 기판에 고체형태로 박막을 제작하는 방식이다. 반면에 CVD는 원하는 재료를 화합물로 만들어 원래의 용융점보다 낮은 온도에서 기체 상태로 기판에 전달하여 열, 빛, 플라즈마를 이용한 화학반응을 통해 고체형태로 박막을 제작한다. 두 방식 모두 물질을 얇은 막 형태로 제작할 수 있다는 점에서는 공통점이 있으나 PVD방식은 특정 방향으로 입자들이 전달된다는 점에서 그림 1과 같이 독특한 형태의 입자 누적이 이루어진다. 이러한 PVD와 CVD로 제작한 박막의 구조 차이점은 3차원 구조체에 박막 형성을 해보면 더 명확하게 드러난다 (그림 2).
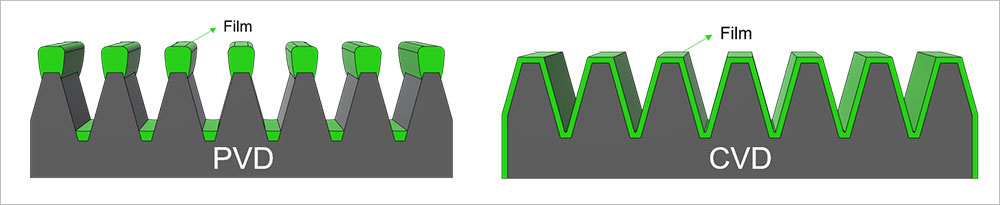
언 듯 보기에는 어떠한 형상에도 균일한 박막을 형성할 수 있는 CVD 기법이 더 우수해 보이지만 연료전지 측면에서는 PVD가 갖는 특징 역시 무시할 수 없다. 일정한 방향으로 입자들이 전달되는 PVD의 물질전달 특징에 공정 압력조절이 더해지면 박막의 밀도를 조절할 수 있다. 연료전지는 기체 투과를 위해 기공이 다수 존재하는 다공성 전극층과, 기체 투과를 방지하는 치밀한 전해질로 구성되어있기 때문에 PVD를 통한 박막의 밀도 조절 기능은 하나의 장비로도 고체산화물 연료전지를 구성할 수 있다는 것을 의미한다. 기본적으로 반도체의 수율 및 품질을 고려하면 최대한 적은 장비를 사용하여 모든 공정이 끝날 때 까지 샘플이 외부에 노출되는 경우를 최소화해야 한다. 반도체 공정을 이용한 고체산화물 제작 역시 이러한 공식에서 자유로울 수 없다. 또한 생산단가를 최소화하기 위해 대면적 증착이 가능하고 높은 생산성이 보장되어야 한다. PVD 공정 중 스퍼터링은 이미 디스플레이에 널리 상용화 되어 이러한 조건들을 충족시킨다. 다만 지금까지 PVD 기술은 치밀막 위주로 연구가 진행되었기 때문에 전극을 위한 다공질 박막 제작을 위한 요소기술을 확보해야 한다.
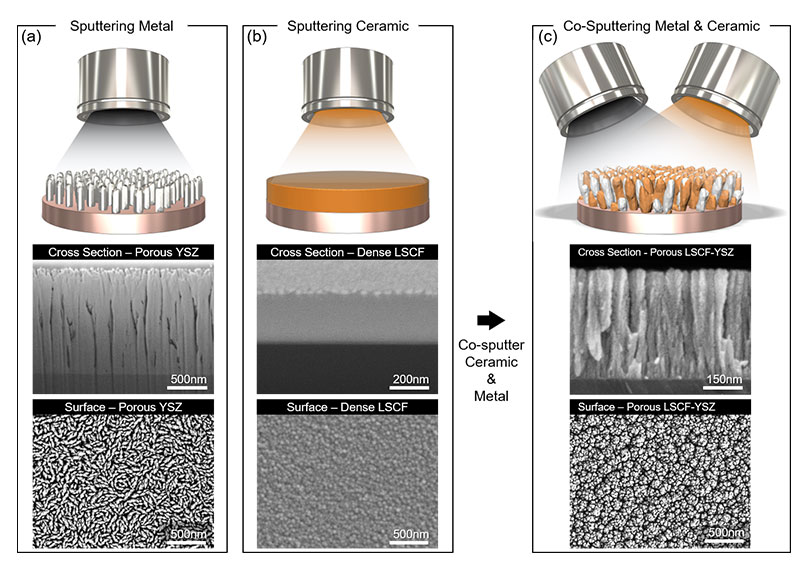
앞서 언급했던 PVD 공법의 공정 압력을 통한 박막의 밀도 조절은 대부분 금속재료를 통해 발견된 현상이다 (그림 3 (a)). 세라믹 재료를 전극으로 사용하는 고체산화물 연료전지에서도 이 공식이 통한다는 보장은 없다. 실제로 대부분의 세라믹 재료는 다양한 압력 하에서 스퍼터링을 진행하더라도 압력에 따른 박막의 밀도차이가 크게 발생하지 않는다(그림 3 (b)). 연료의 원활한 공급을 위해 전극 박막의 공극은 필수적으로 요구된다. 이 문제를 해결하기 위해 고안해낸 방법이 바로 금속과 고체산화물 재료 간 공동 스퍼터링 방법이다(그림 3(c)). 실제 고체산화물 연료전지의 전극은 복잡한 원소로 구성되어 있기 때문에 이들 중 일부를 금속으로 치환하여 세라믹과 동시에 스퍼터링을 진행하면 추가된 금속물질이 공극 확보에 큰 도움을 준다. 추 후 산화 과정을 통해 금속을 원래의 고체산화물로 전환시키면 손쉽게 다공성 고체산화물 전극을 제작할 수 있다. 위 요소기술들을 결합하여 치밀한 전해질과 다공성 전극막이 적용된 연료전지를 제작하고 성능평가를 수행한다면 반도체공정의 고체산화물 연료전지 적용 가능여부를 검토해볼 수 있다.
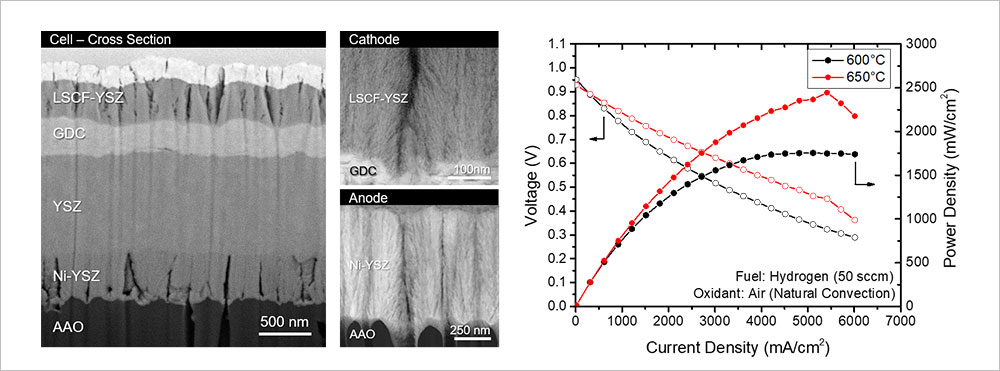
그림 4는 스퍼터링만을 이용해 제작한 고체산화물 연료전지의 이미지 및 성능 곡선을 나타내고 있다. Ni-YSZ와 LSCF-YSZ 전극 물질은 모두 깃털 모양의 3차원 다공성 나노 구조를 보여 우수한 물질 전달 및 촉매성능이 확보되었고, YSZ/GDC 전해질은 1.5um 내외의 매우 얇은 두께에도 치밀한 구조를 보여 이온 전달의 저항을 최소화 한다. 넓은 표면적의 다공성 전극 및 최소화된 이온 전달 거리의 전해질 적용을 통해 성능 역시 600oC와 650oC에서 각각 1.7W/cm2, 2.5W/cm2를 나타내어 같은 재료를 사용한 고체산화물 연료전지 중 가장 높은 성능을 나타내었다[2].
이렇듯 반도체 공정은 기존 고체산화물 연료전지의 성능 한계점을 극복할 수 있는 해결책으로 여겨진다. 실제 산업계 관점에서도 고체산화물 연료전지 전해질 제작의 반도체 공정 적용은 적극적으로 검토되고 있다. 특히 고온 열처리가 필수적인 기존 세라믹 전해질 공정 대비 반도체 공정은 상온 제작이 가능하므로 기판 및 음극 재료의 자유도를 부여하며 제작 시간측면에서 압도적인 효율성을 보인다. 다만 반도체 공정으로 제작한 수nm 단위의 매우 작은 전극 입자는 고온 내구성이 확보되지 않아 이를 해결하기 위한 요소기술[3]과 상용화를 위한 100mm x 100mm 이상의 대면적 스케일 생산 기술 확보는 아직 숙제로 남아있다.
운이 좋게도 우리나라는 연료전지와 반도체 분야에서 세계 정상급의 기술을 보유하고 있다. 아직까지는 연료전지와 반도체간 상이한 재료, 구조 및 작동환경 때문에 활발한 연구 교류는 시도되고 있지 않지만 최근 반도체 기술을 적용한 연료전지의 성능 및 효율향상에 대한 연구가 다수 보고되고 있다는 점은 두 기술간 접점이 근시일내에 발생할 수 있다는 점을 시사한다. 신재생에너지와 반도체라는 4차 산업 핵심기술간 공통분모가 발견된 만큼 다학제간 연구 시너지를 통한 기술 혁신을 기대해본다.
이렇듯 반도체 공정은 기존 고체산화물 연료전지의 성능 한계점을 극복할 수 있는 해결책으로 여겨진다. 실제 산업계 관점에서도 고체산화물 연료전지 전해질 제작의 반도체 공정 적용은 적극적으로 검토되고 있다. 특히 고온 열처리가 필수적인 기존 세라믹 전해질 공정 대비 반도체 공정은 상온 제작이 가능하므로 기판 및 음극 재료의 자유도를 부여하며 제작 시간측면에서 압도적인 효율성을 보인다. 다만 반도체 공정으로 제작한 수nm 단위의 매우 작은 전극 입자는 고온 내구성이 확보되지 않아 이를 해결하기 위한 요소기술[3]과 상용화를 위한 100mm x 100mm 이상의 대면적 스케일 생산 기술 확보는 아직 숙제로 남아있다.
운이 좋게도 우리나라는 연료전지와 반도체 분야에서 세계 정상급의 기술을 보유하고 있다. 아직까지는 연료전지와 반도체간 상이한 재료, 구조 및 작동환경 때문에 활발한 연구 교류는 시도되고 있지 않지만 최근 반도체 기술을 적용한 연료전지의 성능 및 효율향상에 대한 연구가 다수 보고되고 있다는 점은 두 기술간 접점이 근시일내에 발생할 수 있다는 점을 시사한다. 신재생에너지와 반도체라는 4차 산업 핵심기술간 공통분모가 발견된 만큼 다학제간 연구 시너지를 통한 기술 혁신을 기대해본다.
[참고문헌]
• Lee, Y. H.; Chang, I.; Cho, G. Y.; Park, J.; Yu, W.; Tanveer, W. H.; & Cha, S. W. Thin film solid oxide fuel cells operating below 600 C: a review. International Journal of Precision Engineering and Manufacturing-Green Technology 2018, 5, 441-453.
• Lee, Y. H.; Ren, H.; Wu, E. A.; Fullerton, E. E.; Meng, Y. S.; Minh, N. Q. All-Sputtered, Superior Power Density Thin-Film Solid Oxide Fuel Cells with a Novel Nanofibrous Ceramic Cathode. Nano Lett. 2020, 20, 2943−2949
• Lee, Y.-H.; Cho, G.-Y.; Chang, I.; Ji, S.; Kim, Y.-B.; Cha, S.-W. Platinum-Based Nanocomposite Electrodes for Low-Temperature Solid Oxide Fuel Cells with Extended Lifetime. J. Power Sources 2016, 307, 289−296.
![]() |