Extending Our Hands to the Sky: Drone-Based Aerial Robots for Aerial Operation and Manipulation
Professor Dongjun Lee
- The Success of Multirotor Drones in Extending Our Eyes to the Sky: Next Will Be Our Hands
- Key Issues in Drone-Based Aerial Manipulation: Under-Actuation, Flying Time, and Payload Capacity
- Novel Megabot Approach for High Payload, Continuous and Dexterous Aerial Operation
Multirotor drones, often simply referred to as drones (e.g., quadcopters, hexacopters, etc.), are flying robots propelled by multiple rotors (i.e., motors plus propellers), that are colinearly attached to their platform. These multirotor drones have received a lot of attention as systems that capture many aspects of digital transformation (DX) and have been successfully applied to many industrial sectors, particularly in infrastructure inspection, surveillance and reconnaissance, land and terrain surveying, filmmaking, and aerial photography. However, these successful applications are mostly "passive" tasks, extending only our eyes to the sky. The obvious next step is to extend our hands to the sky (i.e., "interactive" tasks), which is the problem of aerial operation and manipulation. Professor Dongjun Lee’s Interactive and Networked Robotics Laboratory (INROL) in the Department of Mechanical Engineering at SNU has been working on this problem for over a decade, from new aerial manipulation robot designs to their sensing/perception, planning/control, and user interfaces.
Multirotor drones are, however, not so suitable for aerial manipulation. In fact, their designs have evolved around camera drones for hobbyists. First, because all their rotors are colinearly aligned, some directions are not actuated, yet, for manipulation and operation tasks, omni-directional force control is typically necessary (e.g., pushing/pulling while rotating in all directions). Due to this issue of "under-actuation", the drones must rotate to translate or translate to rotate. This is far from ideal for interactive operation and manipulation tasks, since, for instance, the drones cannot maintain their attitude while approaching a hole to insert a magazine or while manipulating a tool if side winds blow1. This can be addressed in the camera drones by attaching a gimbal to the camera; however, it is not so for manipulating drones, since there are no robotic arms that are light enough for the drones yet backdrivable to be suitable for force control.
To solve this issue of under-actuation, Prof. Lee’s INRoL has proposed several new aerial robot platforms, such as SMQ (spherically-connected multiple quadrotors2) and ODAR (omi-directional aerial robot3), where the former resolves the issue of side-way under-actuation by attaching multiple quadrotors to a platform via spherical joints so that they can resist side-way winds/forces while leaving the platform’s attitude intact by rotating their attitudes, whereas the latter does so by attaching multiple rotors asymmetrically and also optimally to produce any rotation and translation (or moment and force) totally independently, thereby rendering the platform indeed omni-directional.
Even if these platforms (and also others with, e.g., tilting rotors) could address the issue of under-actuation of multirotor drones, another challenge, perhaps arguably much more difficult to address, still remains. That is, due to the limitation of current propeller propulsion and motor-battery technology, the flying/operation time and the payload (or manipulation force) of rotor-based aerial robots are too restricted to be practically useful (e.g., typically less than 30 minutes for pure flying time with only hundreds of grams-level payload/force4). It is also a well-known fact among researchers in this field that it is fairly difficult to attain robust sensing and control for a single flying aerial robot.
Prof.’s Lee’s INRoL takes an upside-down approach to overcome this fundamental challenge: how about making the robot itself very large to do aerial operation rather than sending a single robot with all the issues as mentioned above? This idea of megabot is, in fact, a dream of many roboticists (e.g., Gundam!). Such megabots, however, cannot be constructed with conventional electrical motors and hydraulic actuations, since they are "internal actuation". Thus, all the weight and force are accumulated at the base, which then needs to be exponentially massive as the robot size increases. To resolve this fundamental issue of scalability of megabot, Prof. Lee’s INRoL proposes a new megabot platform, LASDRA (large-size aerial skeleton with distributed rotor actuation5), which consists of multiple fully-actuated/self-weight-compensating links connected with a joint-locking mechanism so that it can be very long, slender, light, yet dexterous, high-force, and scalable6,7. The current version being built in the lab is 7m long, 15-DOF, total weight lighter than 50kg, and payload around 2kg, with experimental demonstrations underway for the tasks of emergent valve turning and power box lever switching.
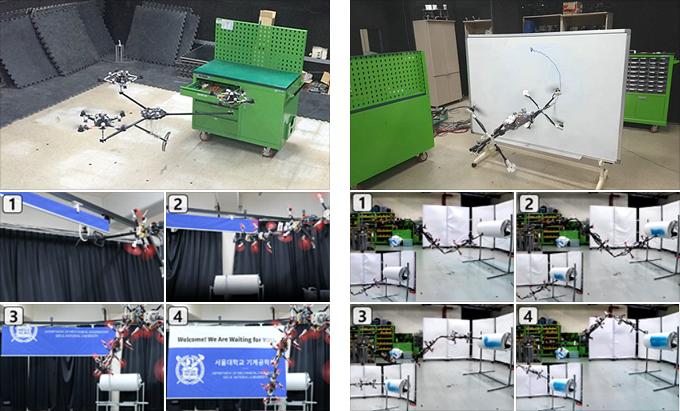
References
- 1 H-N. Nguyen et al, Automatica, 61, 2015
- 2 H-N. Nguyen et al, IEEE Transactions on Robotics, 34(2), 2018
- 3 S. Park et al, IEEE/ASME Transactions on Mechatronics, 23(4), 2018
- 4 A. Ollero et al, IEEE Transactions on Robotics, 38(1), 2022
- 5 H. Yang et al, ICRA, 7017-7023, 2018
- 6 https://youtu.be/Xh7v-6uWfQc
- 7 https://youtu.be/VETL-fqbYik