Successful commercialization in POSCO Gwangyang Steelworks after the large-scale verification process
Removal of fine dust in industrial facilities, published in <Nature Communications> on February 10
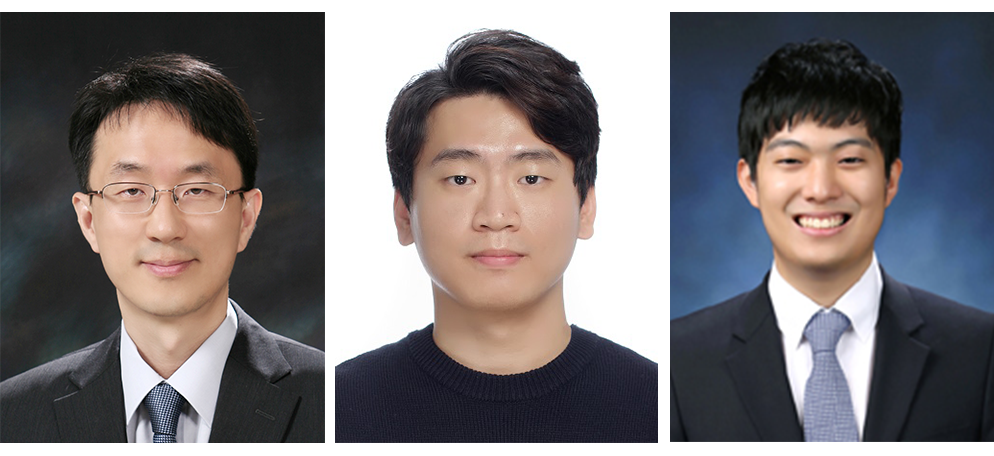
From left, Professor Do Heui Kim, Dr. Inhak Song, and Dr. Hwangho Lee
A source proprietary technology that can effectively remove nitrogen oxides, an environmental pollutant that is known to be the cause of fine dust, was developed by Professor Do Heui Kim's Team of the Department of Chemical and Biological Engineering at Seoul National University.
Through a joint research with the Pohang Research Institute of Industrial Science & Technology (RIST) Fine Dust Research Center, Professor Do Heui Kim's research team developed a vanadium-based catalyst system that can reliably remove nitrogen oxides at low temperatures. With Dr. Inhak Song and Dr. Hwangho Lee as the co-first authors, the results of the study were published online in the international journal <Nature Communications> as of February 10. (Title of Research: Simple physical mixing of zeolite prevents sulfur deactivation of vanadia catalysts for NOx removal)
High temperature nitrogen (N2) and oxygen (O2) from industrial facilities and combustion engines such as power plants, incinerators, and steel mills react to produce nitrogen oxides (NO, NO2). Nitrogen oxide is a well-known environmental pollutant that participates in a photochemical process, resulting in smog, acid rain and fine dust. It is known to cause irritation to the skin and the respiratory tract, leading to fatal diseases. Many countries around the world, including Korea, are putting in effort to regulate these emissions. In particular, as nitrogen oxides in the atmosphere have recently been reported as the main cause of fine dust, there are strict regulations to nitrogen oxide emissions.
Industrial facilities are currently using selective catalytic reduction (SCR) technique by using ammonia (NH3) to remove nitrogen oxides. This technique uses ammonia as a reducing agent to convert nitrogen oxides to nitrogen that is harmless to the human body. Metallic oxide catalysts consisted of titanium oxide (TiO2) and small amounts of vanadium oxide (V2O5) are most commonly used. Vanadium catalysts are widely used because, unlike other catalysts like copper (Cu) and manganese (Mn), they can remove nitrogen oxides without performance degradation due to sulfur dioxide (SO2), which are contained in combustion emissions in areas with temperatures ranging from 300 to 400℃.
Recently, the growing demand for energy conservation in all industries has raised the need for SCR catalysts that can be operated at not just high temperature areas of 300 to 400℃, but also in temperatures below 250℃.
However, at temperatures lower than 250℃, sulfur dioxide (SO2) is converted into the form of highly viscous ammonium bisulfate (ABS) and deposited on the surface of the catalyst, resulting in a new problem that gradually reduces the catalyst's ability to reduce nitrogen oxides. Therefore, in order to successfully utilize SCR technology using vanadium catalysts at low temperatures, the problem must be solved to reduce catalytic activity in the presence of ammonium bisulfate.
The research team was the first to discover that physically mixing zeolites, a porous substance used as adsorbents or catalysts, with conventional vanadium catalysts can selectively absorb ammonium bisulfate deposited on the catalyst's surface to suppress catalytic activity.
Based on this observation, the team proposed a new physical hybrid catalyst that lowers the activation energy with the vanadium catalyst by immediately absorbing ammonium bisulfate deposited in the vanadium catalyst at 220°C.
Through a joint study with Professor Jeong Woo Han of the Department of Chemical Engineering at Pohang University of Science and Technology, the team was also able to theoretically establish that zeolite's special structure has the effect of stabilizing ammonium bisulfate molecules under certain reaction conditions.
This technique was commercialized faster than other existing technologies due to its facile and high performance in manufacturing catalysts. In fact, this newly-developed catalyst has completed its large-scale verification process at the pilot plant, and is currently commercialized and successfully operated at POSCO Gwangyang Steelworks.
"By physically mixing zeolite catalysts, we solved the problem of degradation of vanadium catalysts caused by sulfur. The results are important in that it can theoretically and empirically explain the excellence of the new catalyst. However, the commercialization of a catalyst that was developed through industry-academia joint research holds more meaning." said Professor Do Heui Kim.
The study was conducted with support from POSCO and the Ministry of Science and ICT's leading research center project (Korea University's Super Ultra Low Energy and Emission Vehicle).
For further information, please contact Prof. Do Heui Kim.