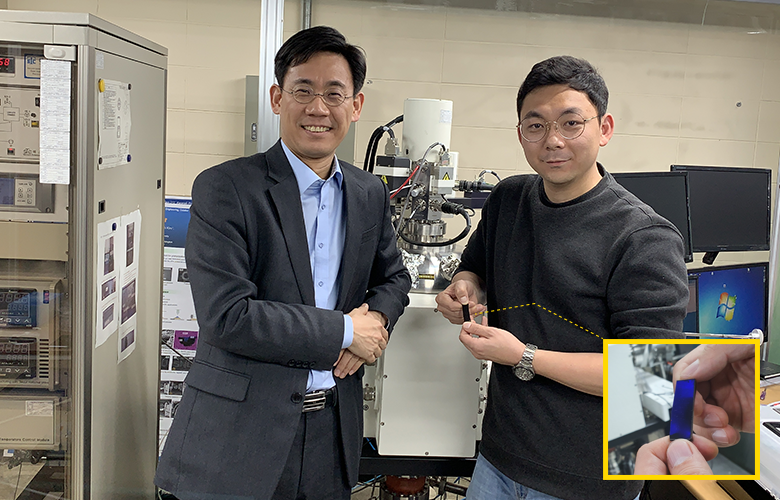
From left, Professor Sung-Hoon Ahn and Doctor Ying-Jun Quan
A research team led by Professor Sung-Hoon Ahn of the Department of Mechanical Engineering has developed a large deformation strain sensor based on structural color.
The structural color-based strain sensor was developed by simulating the micro-/nano-patterns on the surface of a butterfly’s wings or a bird’s feather. The principles of expressing color are divided into traditional methods of using colorants such as pigments and dyes, and structural colors using micro-/nano-structures. Structural colors appear as colors to the human eye by causing interference/scattering when white light is incident on surfaces with micro-/nano-patterns by reflecting or absorbing certain wavelengths of light. The developed structural color sensor can express the strain in the full visible colors of light without an electrical circuit and can measure up to 100% tensile strain and up to 78% shear strain.
Conventional strain sensors have a limited range of deformations that can be measured or require an electrical circuit.
The research team developed a sensor that allows seeing the strain through color change without requiring an electric circuit.
The structural color consists of a two-dimensional nano pattern of similar wavelength as visible light on the surface of the flexible material (PDMS: Polydimethylsiloxane) that reflects a specific color of the visible light region when white light is incident at a fixed angle. When flexible materials are deformed under force, the distance between the surface's nano pattern changes, therefore changing the reflected color. While previous research on measuring strain through structural color-based sensors stopped short at an explanation of a phenomena, this study proposes a formulaic model between wavelengths and strain and makes the application as a strain sensor possible. Additionally, the research team developed a diffractive structural color-based strain sensor that can measure tension, compression, and shear for the first time using various designed patterns.
The first author Dr. Ying-Jun Quan (Institute of Advanced Machines and Design) stated that "The developed strain sensor was integrally manufactured by a soft nanoimprinting process, and suitable for mass production because it does not require any additional processes, and it has the advantage of having a better durability than other multi-material structurally colored nano pattern structures because of one-body diffractive nanostructure array which is PDMS."
The corresponding author Professor Sung-Hoon Ahn said, "We expect that the developed sensor can be used for the likes of soft robots or wearable devices with large deformations because it can measure mechanical deformations visually or through changes in color on camera without additional electronic circuits and wires being connected."
The research findings were published online on the <
ACS Publications> on April 10th and was selected as the cover paper for the May issue of ACS Nano.
For further information, please contact Prof. Sung-Hoon Ahn.